Dicke von Stahlblechen mit Radar kontrollieren
Beim Walzen von Stahlbändern muss sichergestellt werden, dass diese die gewünschte Dicke haben. Bislang ist dies in Anwendungen, wo widrige Umweltbedingungen wie Dampf, Zunder und Spritzwasser vorherrschen, nur mit ionisierender Isotopen- oder Röntgentechnologie realisierbar. Ein neuartiges Radarsystem misst die Dicke verschiedener Messgüter dagegen im Submillimeterbereich auch bei widrigen Bedingungen – und dies sogar ohne ionisierende Strahlung.
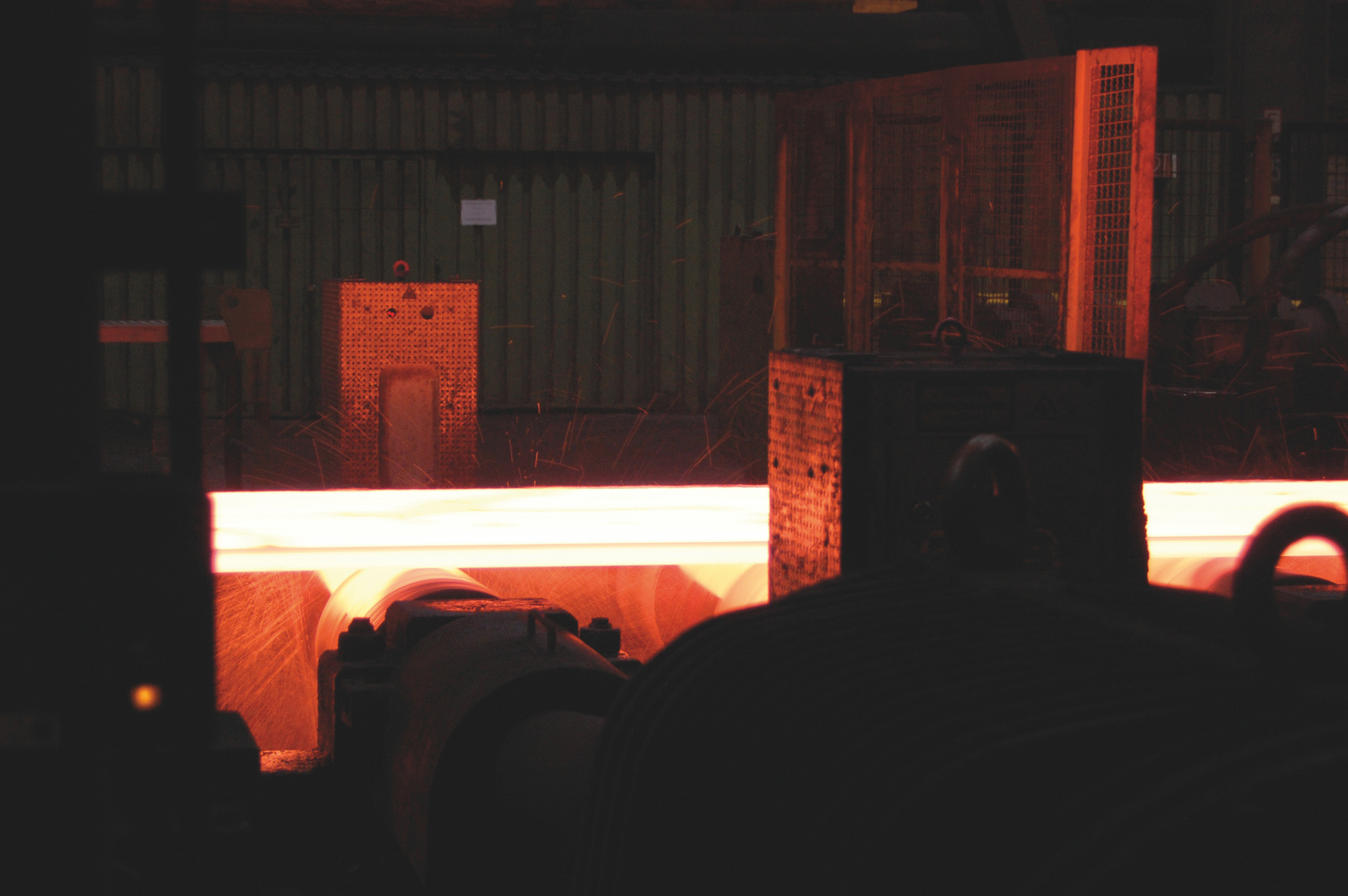
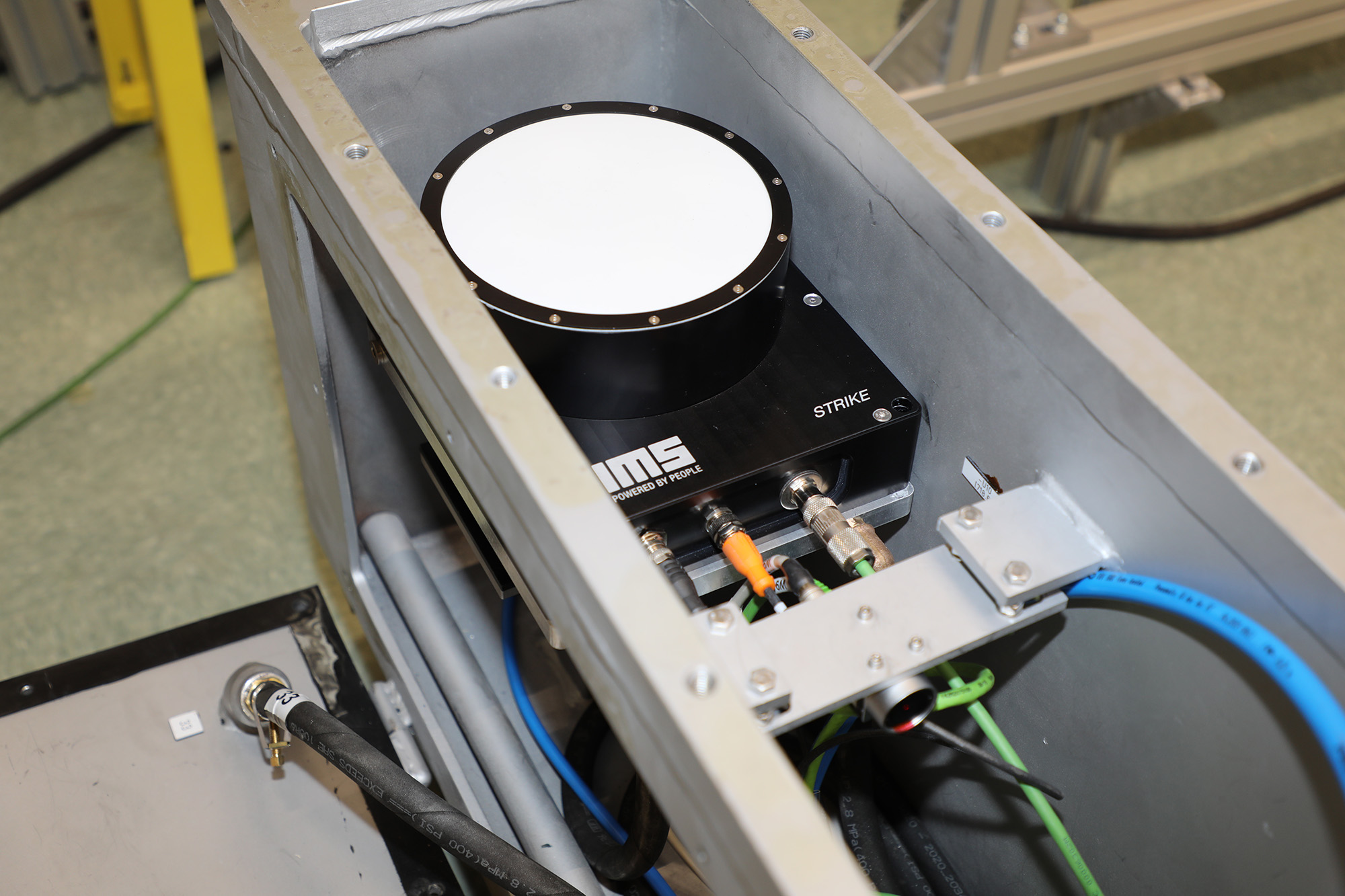
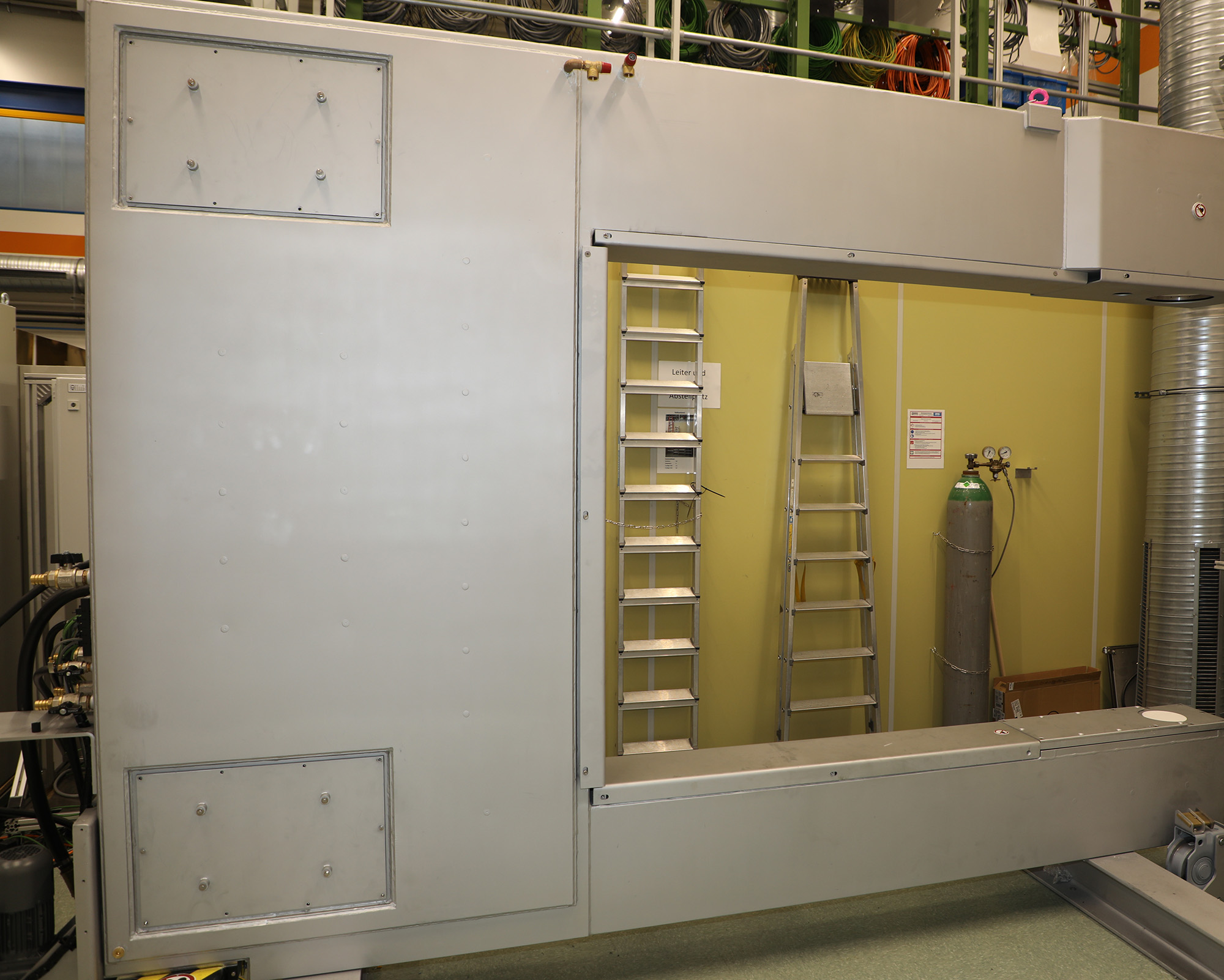
Sei es für Autos, sei es für das Verkleiden von Bauteilen: Stahl wird vielfach in Form von Bändern weiterverarbeitet. Dazu werden die Brammen aus Rohmaterial in Walzwerken schrittweise zu langen Bändern ausgewalzt und für den Transport zu Coils aufgerollt. Elementar beim Walzprozess ist: Das produzierte Band muss die vorgegebene Dicke haben, und zwar auf ganzer Länge und ohne größere Schwankungen. Zur Messung der Band- bzw. Blechdicke werden derzeit überwiegend Systeme eingesetzt, die auf Isotopen- und Röntgenstrahlung basieren. Hierdurch entsteht aber zusätzlicher Aufwand – schließlich sind Strahlenschutzmaßnahmen nötig. Zudem stoßen diese Systeme bei sehr dickem Material an ihre Grenzen. Optische Systeme reagieren wiederum empfindlich auf Wasserdampf und Nebel.
Daher hat das Fraunhofer FHR zusammen mit der IMS Messsysteme GmbH die erste auf Radarsensorik basierende Dickenmessung für Warmwalz- und Grobblechstraßen entwickelt. Die Vorteile: Radarsysteme benötigen nur geringe Sendeleistungen, so dass keine zusätzlichen Sicherheitsmaßnahmen erforderlich sind. Im Gegensatz zu optischen Systemen sind sie unempfindlich gegenüber harschen Umweltbedingungen wie Nebel, Spritzwasser und Staub. Dabei erfordern Radarsysteme kaum Instandhaltungsarbeiten. Die Elektronik ist wartungsfrei, lediglich das Sichtfenster des Sensors muss von Dreck, Zunder und Walzemulsion freigehalten werden.
Der STRIKE-Sensor liefert auch bei widrigen Umweltbedingungen belastbare Ergebnisse
Der am Fraunhofer FHR entwickelte Strike-Sensor wurde bereits in eine Dickenmessanlage der IMS integriert. Mit ihm lassen sich die Messgutdicken selbst in dampfigen, nebligen, staubigen und sehr aggressiven Umgebungen zuverlässig und genau messen. Das Messsystem besteht aus zwei vierkanaligen Radarsensoren, die gegenüberliegend in einem C-Bügel montiert sind. Die beiden Sensoren senden Radarstrahlen aus, die vom durchlaufenden Messgut reflektiert und vom Sensor wieder empfangen werden. Da dies zeitgleich von unten und oben geschieht, lassen sich aus Referenzkalibrationsdaten die Abstandswerte berechnen und somit die Dicke des Bandes bestimmen. Eine Herausforderung: Das Stahlband bewegt sich ständig mit einer Geschwindigkeit von bis zu 20 km/h unter den Sensoren hinweg, die Messrate muss daher entsprechend hoch und die Messung auf Ober- und Unterseite synchron sein – nur so lässt sich die Dicke des Messguts fortlaufend mit hoher Genauigkeit erfassen. Der entwickelte STRIKE-Sensor gewährleistet dies: Er arbeitet derzeit mit einer Messrate von einem Kilohertz. Das gesamte Messystem liefert also achtmal 1000 synchron erfasste Distanzmesswerte pro Sekunde.
Die Auswerteeinheit basiert auf FPGAs – also auf programmierbaren digitalen Bausteinen. Sie ist direkt im Sensor integriert und erlaubt eine vollständig edge-gestützte Auswertung. Die gesamte Signalverarbeitung der Radarsignale findet auf dem FPGA statt – auch die Ansteuerung der Radarchips und die Kommunikation mit der zentralen Recheneinheit der IMS Messsysteme GmbH wurde in dieser integrierten Logikeinheit implementiert. Somit kann die Dicke des Stahlblechs mit einer Rate von einem Kilohertz in Echtzeit gemessen werden.
Die Genauigkeit der Dickenbestimmung liegt bei ebenen laufendem Band bei unter 100 Mikrometern. Ist die Bandoberfläche beispielsweise aufgrund der Bandbewegung oder Wellenbildung geneigt, werden mittels der Vierer-Anordnung die Winkelauslenkungen bestimmt und korrigiert. Die Messgenauigkeit der Dickenmessung kann somit unter +-150µm erhalten werden. Der Messbereich der möglichen Winkellagen des Bandes liegt bei der genutzten Antennengeometrie bei von bis zu 3 Grad in jede Richtung.
Der Sensor ist fertiggestellt. Derzeit befindet er sich in der Testphase, um Ausfallsicherheit garantieren zu können. Ist diese abgeschlossen, wird die IMS Messsysteme GmbH die Sensoren in ihren Aufbau integrieren und eine erste Messanlage an ein US-amerikanisches Walzwerk ausliefern. Natürlich ist die Anwendung des Sensors keineswegs auf Walzwerke begrenzt – vielmehr lässt er sich überall dort einsetzen, wo Distanzen und Winkel bestimmt werden müssen.