Detecting defects in glass fiber reinforced plastic in-line
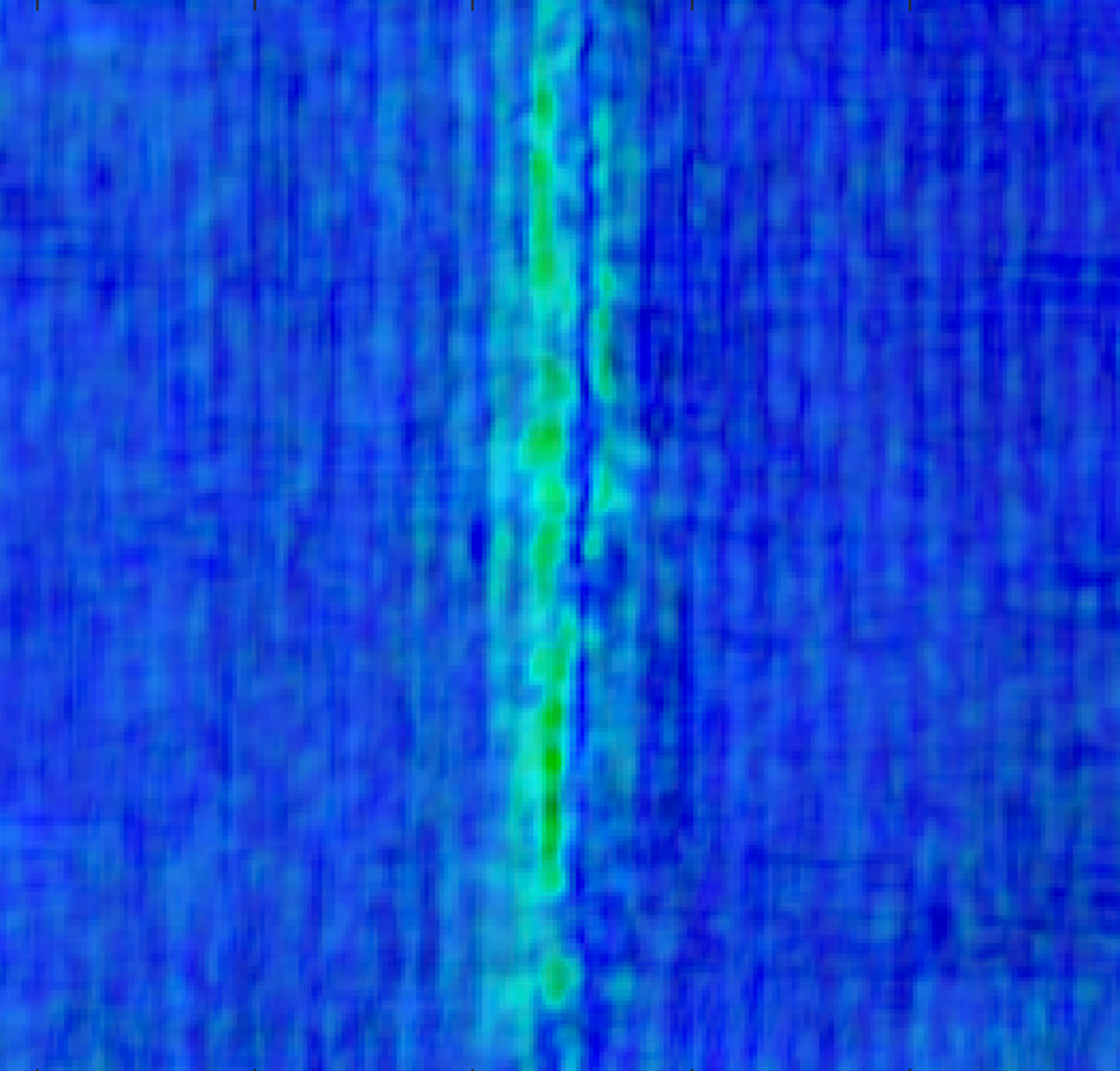
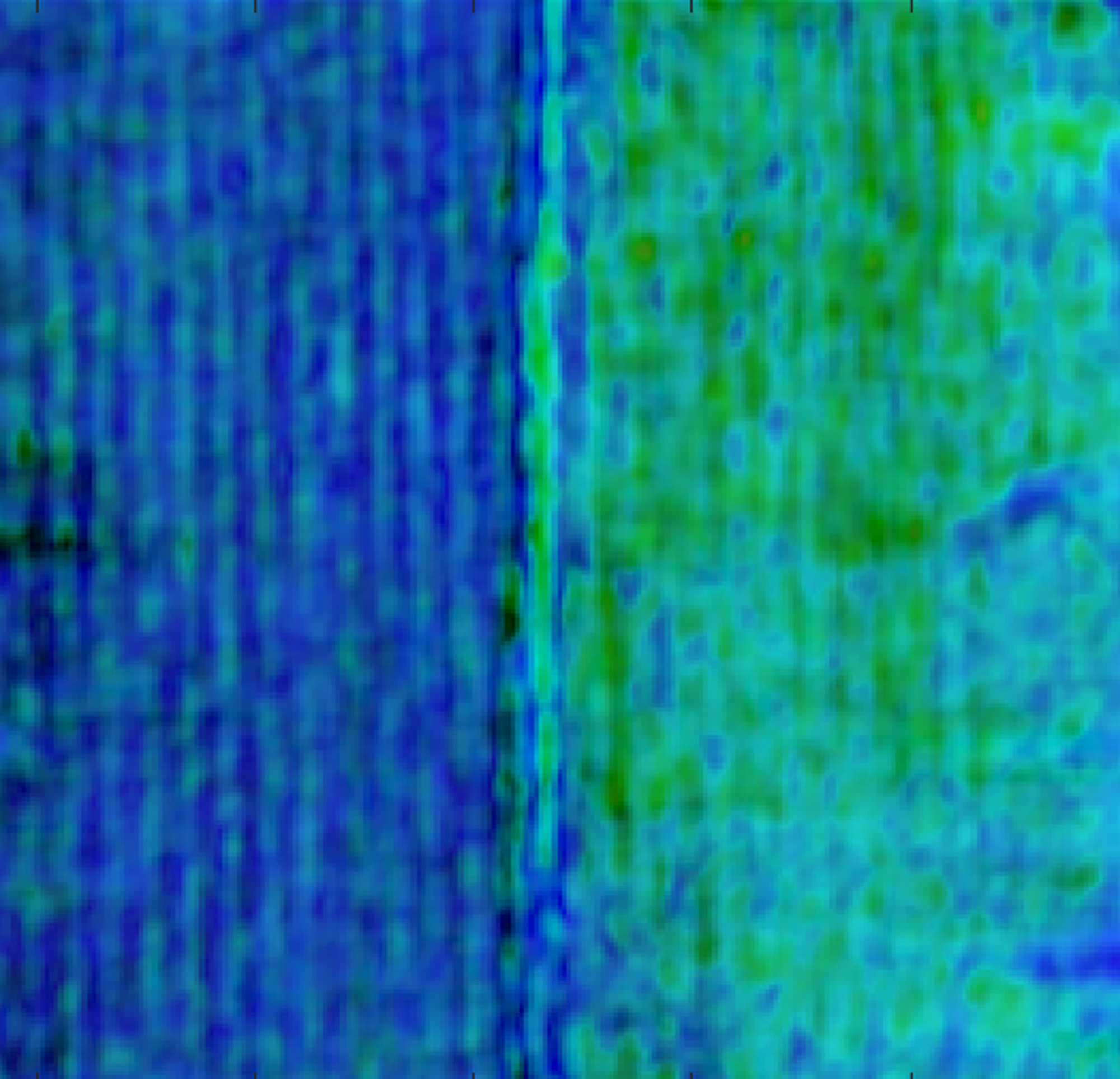
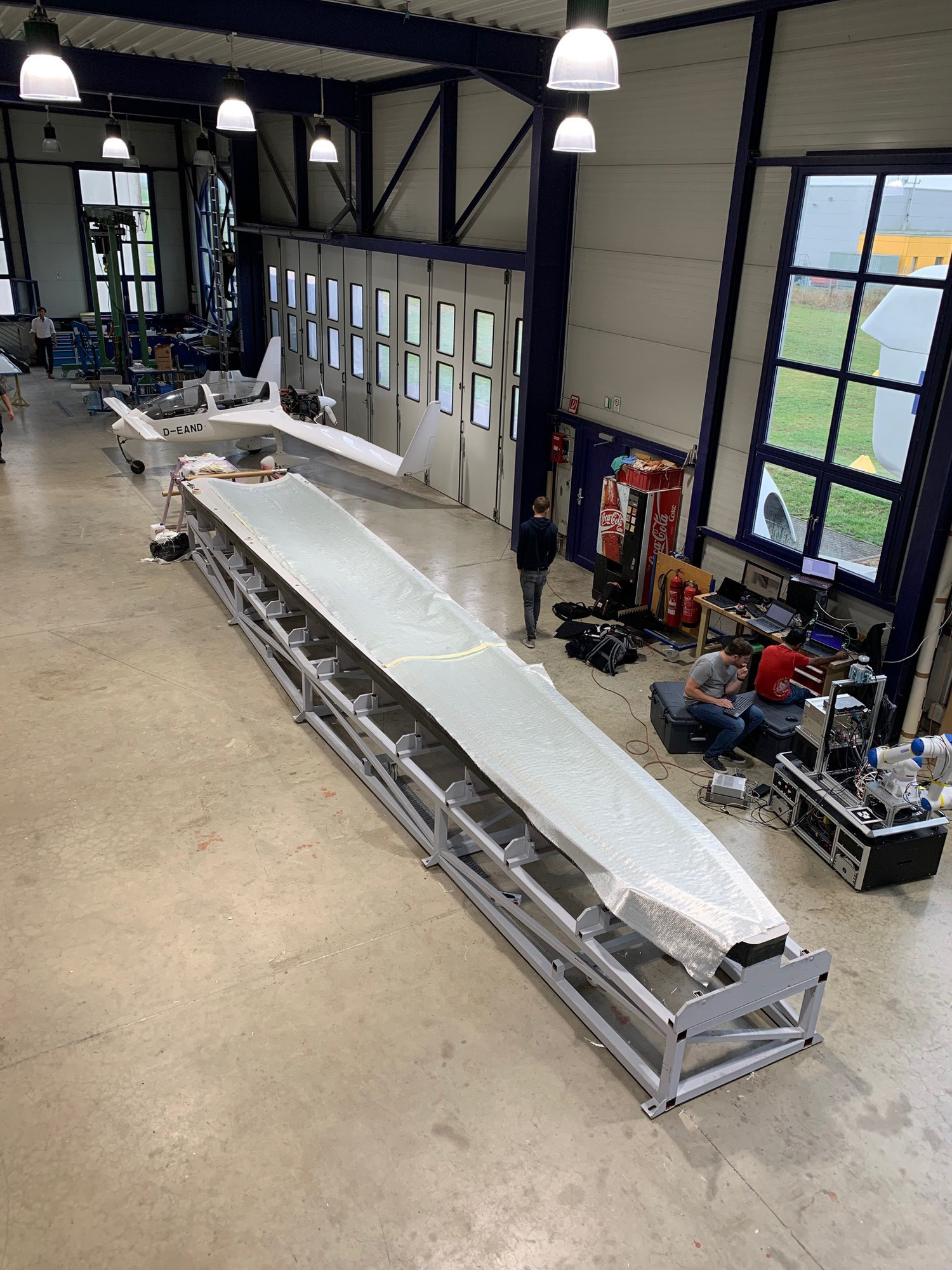
Precision is required in rotor blade production: The individual glass fiber mats must be precisely aligned. For the first time, defects can be detected automatically, non-destructively and throughout the entire volume using a fully polarimetric radar - automatically during production.
Humans do not have X-ray vision. But it would sometimes be practical to be able to look inside things: For example, in the field of manufacturing rotor blades, which are made of glass-fiber-reinforced plastics and are used in wind turbines. In this process, various glass fiber mats are placed on top of each other, placed under vacuum and bonded with resin. However, if errors occur during the positioning of the glass fiber mats, for example if there are waves in a mat or the fibers are misaligned, this can have a negative effect on the mechanical properties of the manufactured component. However, such defects cannot be seen with the naked eye, especially if other glass fiber mats are stacked on top of them and the whole thing is vacuumed and pressed together in a very confined space. The only inspection option at present is manual inspection, whereby defects are only ever detected in the upper layer, if at all.
What remains closed to human vision, however, can be detected by a fully polarimetric radar: It detects defects already during production, non-destructively and automatically, across all layers. It was developed by researchers at Fraunhofer FHR in the publicly funded project Fiberradar (NRW-Leitmarkt), together with Aeroconcept GmbH, Ruhr University Bochum and Aachen University of Applied Sciences. The radar has a total of four channels, two for transmitting and two for receiving - instead of the usual one. This means that four possible combinations are available to elicit information from the rotor blade.
First successful measurements
A demonstrator has already been able to show what the system can do - even in a production environment. To do this, the researchers mounted a robotic arm on a mobile platform, which in turn holds the radar device. This setup scanned the entire blade tip, one-eighth of a rotor blade, and in this way allowed the fiber structure of the fiberglass composite to become visible. While the hardware components were developed by the partners, Fraunhofer FHR contributed its expertise in the algorithms needed for the evaluation. For example, the researchers succeeded in significantly increasing the image quality by adapting existing algorithms from polarimetric imaging to fiber composites on the one hand, and developing new algorithms for handling highly refractile materials specifically for this application on the other.
For the test measurements, Aeroconcept GmbH specifically introduced defects into the wing tip that are more likely to occur during production: Misalignment defects, where fibers in a layer are misoriented. Undulations, where invisible waves occur in the layers. Half lengths, where the fiber layer stops in the middle of a layer. The system was able to reliably detect all of these errors. Two of the four channels in total, the cross-polarizations, scored well in detecting undolations and half-lengths. By combining the channels, the researchers can present the results to the user in a unified overview. The half-lengths were particularly easy to detect when the fiber direction changed, but when the direction was the same, the method also gave very good results. The system also detected angular errors very well: Defects of 10 and 20 degrees could be clearly detected even in deep layers - although the defects were covered by several layers. Thus, for the first time, defects could be detected via radar during the manufacturing process.