3D Printed multimodal antennas
How good of a resolution a radar system has is primarily determined by the radar system's bandwidth. Conventional antenna manufacturing processes, however, are maxed out when it comes to the bandwidth. In contrast, 3D printed antennas promise a higher bandwidth and, with this, an improved resolution. In addition, broadband antennas make it possible to combine the apertures of different systems.
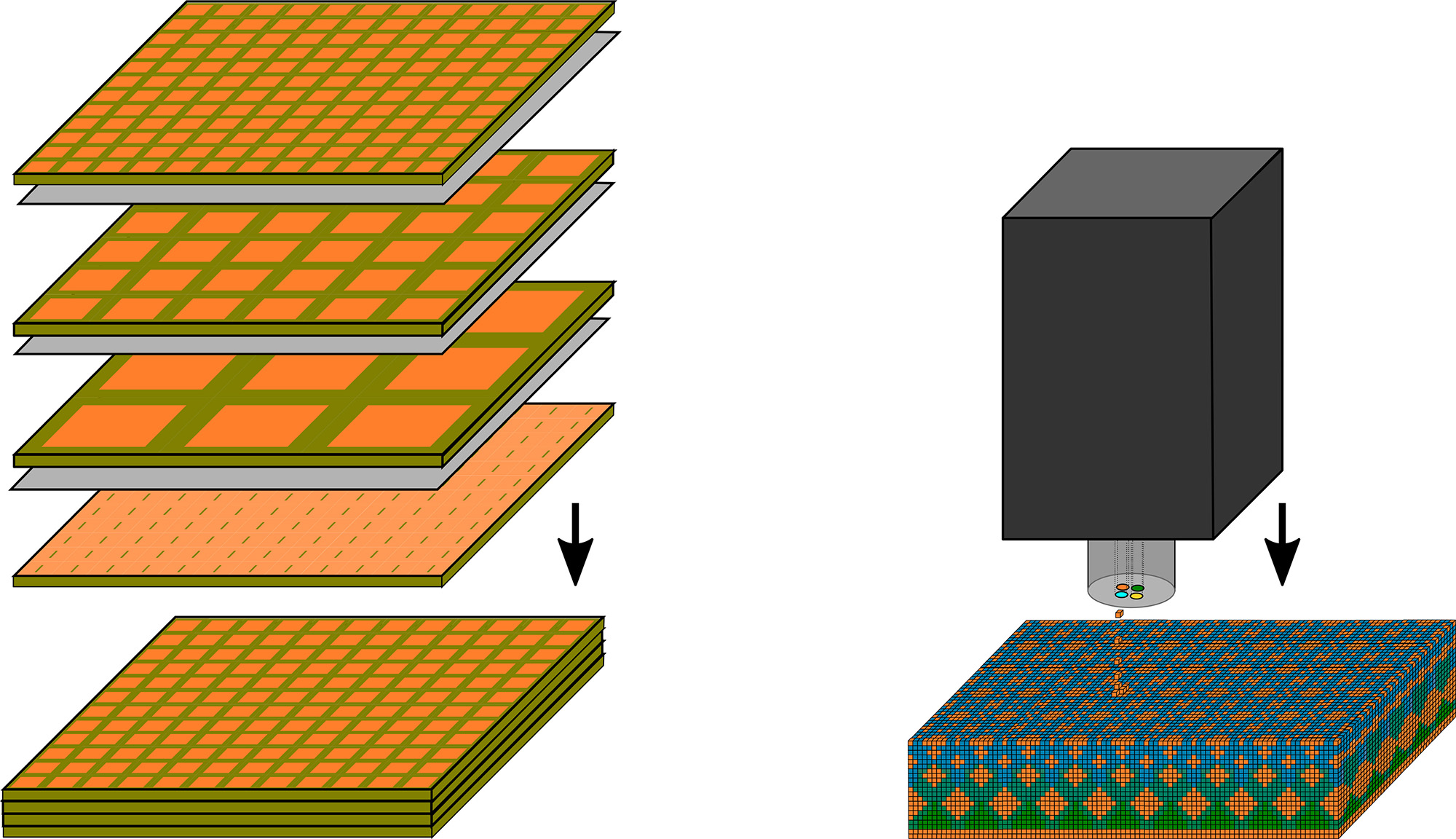
Fighter jets, drones, and frigates have one thing in common: Numerous different systems are installed on them, each with its own antenna and there are up to 150 antennas on some frigates. On the one hand, this can make things quite tight and on the other hand, the antennas influence each other. If antennas with a higher bandwidth could be used, it would be possible to combine several antennas. A higher bandwidth is desirable for other reasons as well: For radar, the bandwidth plays a key role in determining the resolution and for communication applications, it determines the channel capacity. Multimodal antennas, i.e. a combination of antennas, offer a solution. The catch here is this: They are hard to produce using conventional manufacturing processes such as circuit boards since they seem to have reached their limit in terms of producible bandwidth.
3D Printing Allows an Improved Utilization of the Volume – Thus Allowing Potentially for Higher Bandwidths
Therefore, Fraunhofer FHR is breaking new ground and betting on 3D printing for the production of multimodal antennas. In qualitative terms, it is a known fact that a certain volume has a fixed bandwidth limit. In other words: the larger the antenna, the larger the possible bandwidth. But how can we make better use of the existing volume and achieve the highest possible bandwidth for small antennas as well? This is where 3D printing comes into play: Since we are dealing with the monolithic area – in contrast to circuit boards – it is possible to directly use the height and thus obtain higher bandwidths. This provides a better variation of the material parameters. While for simple printing processes, the same material is used for each print, the effective material parameters can be set, e. g. using targeted air inclusions. A stable process is still missing: The printing quality has to be good in the millimeter range as well, and the suitable material is also needed. The available materials are not characterized for this purpose. Fraunhofer FHR is characterizing purchasable materials for the high frequency area, optimizing them for this where appropriate.
In the long term, 3D printing will not only allow for different antennas to be combined but also for the antenna and the feeding network from which it obtains its energy. Conformal antennas, such as the ones integrated in an aircraft fuselage, can also be produced very well using 3D printing – the required curvature can be achieved directly with the print.