3D printed antenna: High complexity – simply manufactured
High-performance radar systems on board of unmanned aircraft as well as in vehicles of all kinds require systems that are as light and compact as possible. With this in mind, researchers at Fraunhofer FHR are developing radar-compatible 3D-printed waveguide-based antenna array systems that are significantly more compact and easier to manufacture than their metal-based counterparts.
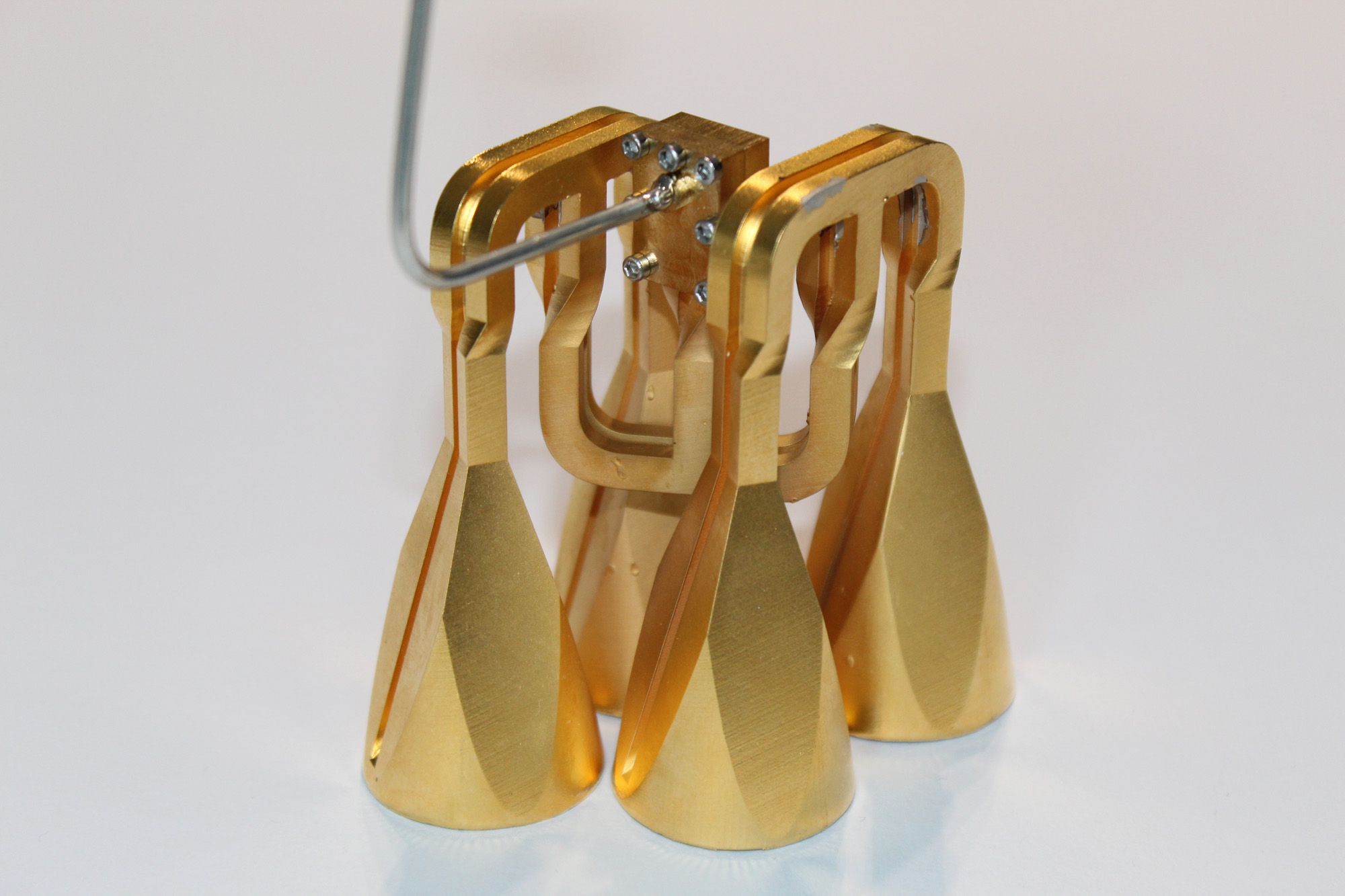
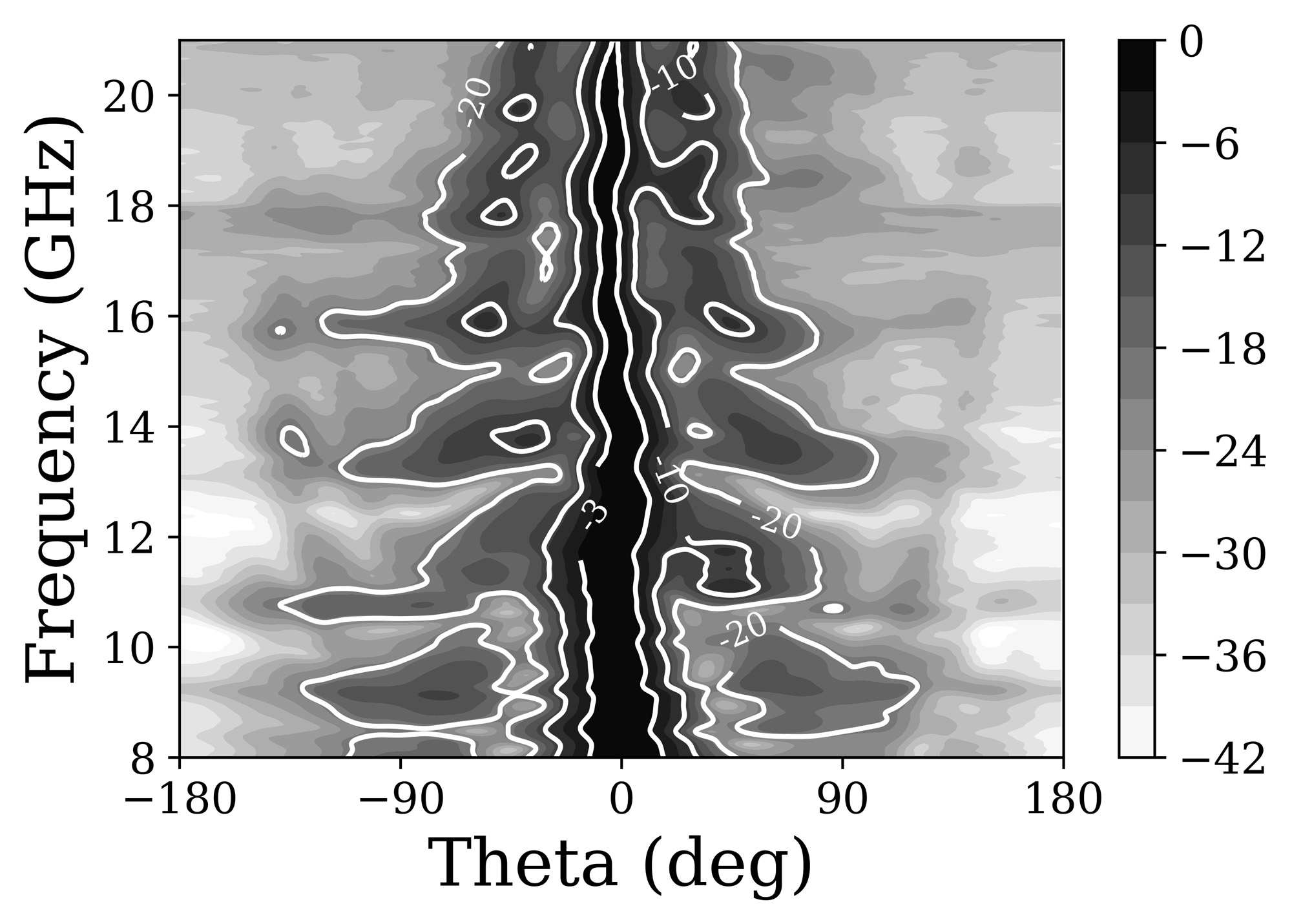
Be it defense, satellite, medical or automotive applications, the next generation of radars will require more bandwidth, range and power – which can only be achieved with highly complex solutions – while being lightweight, compact and cost-effective. Sounds hardly feasible? So far, this impression has been pressing: After all, waveguide-based antenna arrays usually consist of many small and heavy parts normally made of metal, which are also extremely complex to manufacture and hence cost-intensive.
3D printing technology offers a way out. Researchers at Fraunhofer FHR are relying on it to develop new waveguide antenna array designs consisting of several radiating elements with high bandwidth. The array comes from the 3D printer and is made of plastic – the resulting antenna arrays are therefore much lighter than their metal counterparts. Another highlight is that despite the complex structure, the antenna can be manufactured in just one step, which makes production much more easy and cost-effective. By using 3D printing technology, more compact waveguide antenna array designs can also be realized without sacrificing system efficiency.
Since the plastic itself does not have the electromagnetic properties required by an antenna, the researchers galvanize it with a layer of copper and nickel. The unique properties of the developed process allow the metallization layer to be applied only to the outer surface – further simplifying the manufacturing process and eliminating the need to deal with the inside parts of the structure. The applied copper layer allows the electromagnetic phenomenon to occur, while the nickel stabilizes this layer and protects it from oxidation and corrosion. The result is already impressive: The 3D-printed antenna, which operates in a frequency range of 8 GHz to 21 GHz and has a directivity of 17 dBi, has already been successfully tested at Fraunhofer FHR.
Currently, researchers at FHR are looking forward to enhancing the performance of the 3D printed structures by investigating novel manufacturing approaches and testing new materials to apply to their designs.